The trucking industry is notorious for its high operational costs, which have driven many businesses to the brink of bankruptcy. From fuel expenses to maintenance costs, the financial burden associated with running a trucking business can quickly accumulate, leading to unsustainable operations and financial distress.
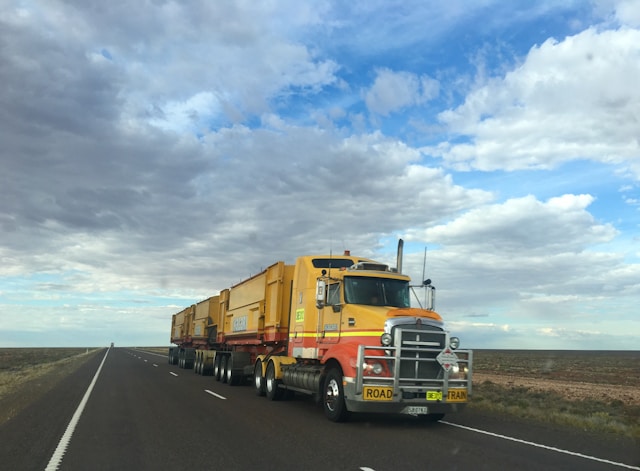
Trucking businesses face a multitude of expected costs that are inherent to the industry. These include:
- Trucks endure extensive wear and tear from constant use, necessitating regular maintenance and repairs to ensure operational efficiency and safety. From engine overhauls to tire replacements, maintenance costs can escalate rapidly, particularly for aging fleets or vehicles subjected to harsh driving conditions.
- Truck drivers play a pivotal role in the success of a trucking business, but compensating them fairly comes at a cost. Wages, benefits, and associated payroll taxes constitute a significant portion of operating expenses, making labor management a critical aspect of financial planning.
- Investing in modern equipment and technology solutions, such as GPS tracking systems and electronic logging devices, is essential for enhancing efficiency, compliance, and safety. However, these investments require substantial capital expenditure, adding to the overall cost burden.
Given the myriad expenses associated with running a trucking business, effective cost management is paramount to maintaining profitability and sustainability and all of this must be taken into account when providing trucking quotes to potential customers.
While on the subject of cost management, it’s essential to address the often-overlooked expenses that can have a crippling impact on trucking businesses without proper attention.
The importance of fuel monitoring
Fuel is one of the most substantial expenses for any fleet business. However, while fuel costs are expected, without monitoring fuel usage in fleets, fuel costs can quickly spiral out of control. Implementing a robust fuel monitoring system is essential for tracking fuel usage accurately and identifying areas of waste.
By monitoring fuel consumption in real-time, fleet managers can detect anomalies such as excessive idling, unauthorized vehicle use, or inefficient routes. This can also be a useful tool to identify issue with vehicle engine.
Break-ins: Protecting your fleet
Break-ins pose a significant threat to fleet businesses, resulting in both financial losses and operational disruptions. Securing vehicles and cargo is paramount to safeguarding assets and maintaining operational continuity.
Investing in security measures such as GPS tracking, alarms, and surveillance cameras can deter potential intruders and provide valuable insights in the event of a break-in. Additionally, training drivers to be vigilant and park in secure locations, such as with access control and locked gates, can minimize the risk of theft and vandalism.
What’s the true cost of break-ins? Break-ins can result in various costs, including stolen goods, vehicle damage, and potential liabilities from injuries or accidents. Securing parking facilities and implementing robust security protocols can mitigate these risks and protect the business’s assets.
Insurance premiums: They don’t have to be that high
Of course, you can expect to pay insurance premiums. But truck fleet insurance premiums can be a significant expense for businesses. Thankfully, there are ways to keep costs manageable. For a start, you should work with specialist fleet insurers for your area and implement risk management strategies can help mitigate insurance risks and reduce premiums.
What factors can drive premium costs high? Factors such as driver safety records, vehicle maintenance practices, and cargo security measures can influence insurance premiums. By prioritizing safety, implementing preventive maintenance programs, and investing in driver training, businesses can demonstrate reduced risk and negotiate lower insurance rates.
Routes and itinerary costs
Inefficient route planning can result in increased driving times, higher fuel consumption, and missed delivery opportunities. By optimizing routes and itineraries, businesses can maximize efficiency and minimize costs.
The key here is to plan routes that minimize driving distances and prioritize delivery spots. This will instantly help reduce fuel consumption and improve overall productivity. Additionally, leveraging technology solutions such as route optimization software can streamline the planning process and identify the most efficient routes.
What are the costs of Ineffective route planning? To put it in simple terms, this can lead to longer delivery delays, increased fuel costs, and dissatisfied customers.
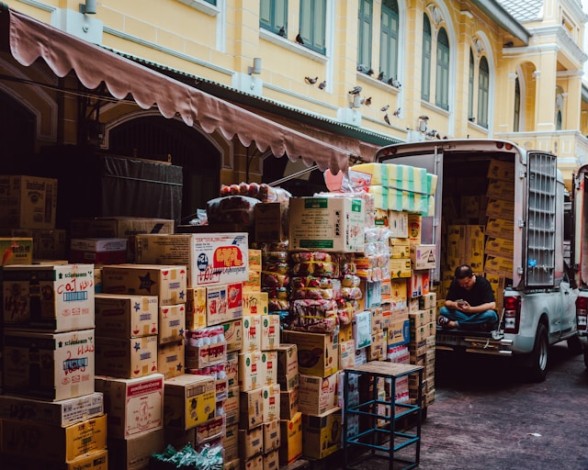
Loading and unloading processes
Inefficient loading and unloading processes can result in wasted time, damaged goods, and increased risk of injuries. Fleet businesses need to streamline their operations by Implementing standardized loading and unloading procedures. This can include training personnel on proper handling techniques, and investing in equipment such as forklifts or loading docks.
The cost of Inefficient loading and unloading processes can be high, leading to increased labor costs, goods replacement, and potential liabilities from workplace injuries.
In conclusion, while managing a fleet business comes with its challenges, addressing these often-overlooked costs can lead to significant savings and operational improvements. There is a variety of different costs to consider, and it’s worth thinking outside the box to tackle unexpected costs. By implementing proactive strategies and leveraging technology solutions, fleet managers can mitigate risks, reduce expenses, and enhance overall business performance.